Un nouveau système de transport autonome vient prouver l’avance de Roto sur nombre de ses concurrents lorsqu’il s’agit d’utiliser les dernières technologies pour améliorer l’efficacité des processus.
Notre site de production de Leinfelden-Echterdingen, près de Stuttgart, comptait déjà des systèmes de transport sans conducteur au sein de l’usine et des zones de stockage. Désormais, un nouveau train logistique 100 % autonome, composé d’une unité de traction sans conducteur et de deux remorques, déplace les produits finis d’un bout à l’autre du site. Ce système peut charger des palettes, les emmener à destination et les y décharger, le tout sans supervision humaine.
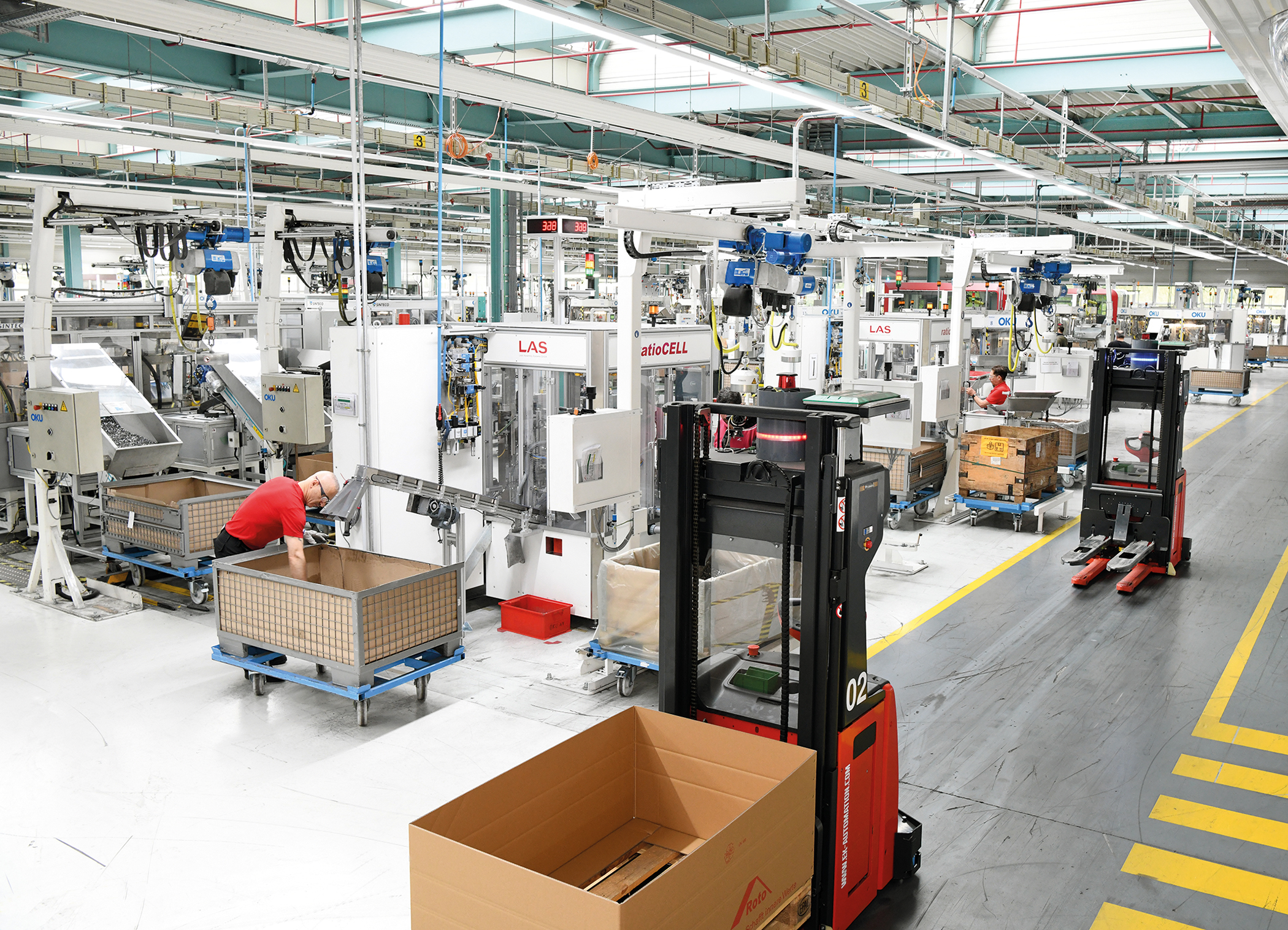
Cette innovation s’inscrit dans le plan à long terme « Logistics Strategy 2025 » de Roto, lancé en 2019 et qui vise le déploiement de divers projets d’automatisation et de numérisation, en vue d’améliorer le flux des produits sur le site. En 2020, Roto a mis son premier processus de transport autonome en service à Leinfelden. Ce système installé en intérieur emmène des boîtes en carton vides jusqu’à la zone de production, où elles sont remplies de composants neufs. Ensuite, il ramène les boîtes à la zone de stockage intermédiaire.
Après avoir éprouvé ce système, nous sommes passés à l’étape suivante : mettre en service un service de transport extérieur qui soit aussi capable d’opérer en parfaite autonomie. Notre fournisseur Neumaier Industry GmbH nous a conseillés pour ce projet, afin d’évaluer nos exigences et de concevoir un véhicule qui puisse remplir tous les critères opérationnels et sécuritaires de Roto.
L’unité de traction et les remorques sont dotées de capteurs de sécurité qui surveillent l’espace autour du véhicule. Ils détectent jusqu’aux plus petits obstacles et évitent tout risque de collision avec des personnes. Si le système détecte une anomalie, le train s’arrête immédiatement et ne repart qu’une fois l’obstacle supprimé, ou une fois que plus personne n’est sur son chemin.
Le train conserve son cap grâce à la géonavigation et se déplace à une vitesse maximale de 5 km/h.
La communication entre le nouveau train logistique extérieur et les autres systèmes logistiques a été coordonnée avec la plus grande précision. Le train extérieur collecte les produits finis dans la zone de stockage intermédiaire, où le système de transport intérieur autonome travaille de concert avec plusieurs systèmes manuels. Une coordination précise et sûre est donc indispensable.
Le chargement et le déchargement des palettes s’effectue à l’aide d’une technologie de convoyeur à rouleaux électrifié.
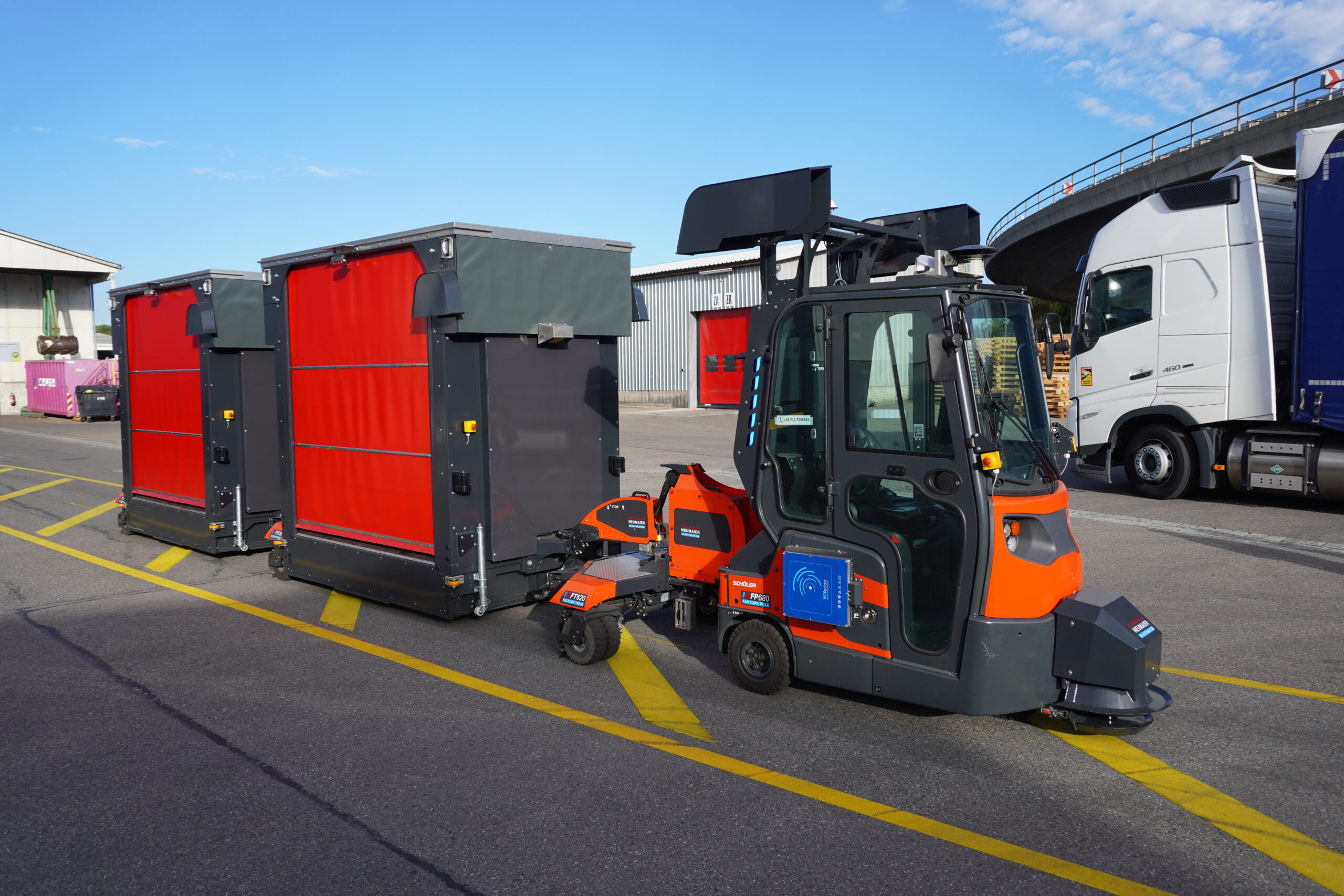
Cette technologie se retrouve à la fois sur les convoyeurs et dans la zone logistique, ainsi que sur les deux remorques du train logistique extérieur, chacun pouvant accueillir deux palettes en même temps à tout moment.
Stefan Duge, Intralogistics Project Manager chez Roto Leinfelden : « Depuis que ce projet a été bouclé, il nous a permis d’optimiser l’organisation d’une grande partie de nos flux de matériel internes. Les deux systèmes de transport sont extrêmement flexibles et garantissent des flux de matériel continus au sein de notre production et de notre intralogistique. »
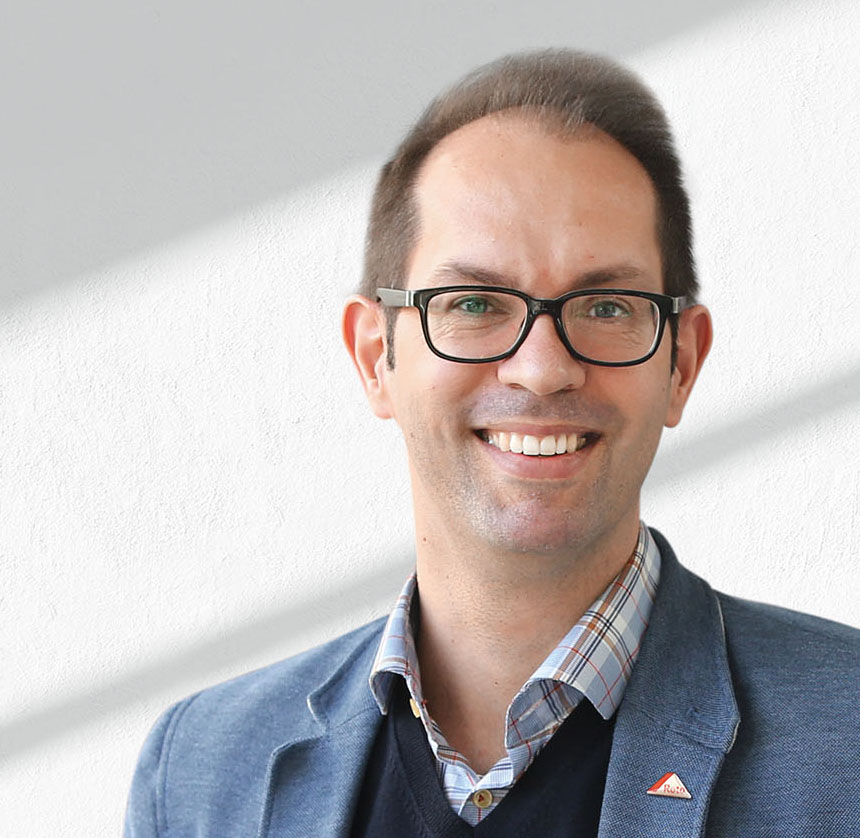
Il explique ensuite comment le système offre une valeur ajoutée aux clients en accélérant la disponibilité des produits. « Ces deux systèmes sont indépendants du nombre de shifts », ajoute-t-il. « Autrement dit, nous réduisons nos temps de passage en continuant à transporter des pièces et du matériel 24/7, sans interruption, même lors des pics de capacité de production ou durant les vacances. Résultat : nos produits finis sont distribués plus vite et sont donc plus rapidement disponibles pour nos clients. »
Le train logistique extérieur peut être contrôlé manuellement, mais la probabilité que ce soit nécessaire est faible. En effet, il est conçu pour fonctionner dans toutes les conditions météorologiques et ne nécessite qu’une maintenance par an.
Ayant été conçu spécifiquement pour le site de Roto Leinfelden, ce nouveau système ne peut pas être reproduit de manière identique dans d’autres lieux, mais nous espérons déployer une technologie similaire sur d’autres sites de production Roto à moyen terme.
Dans le cadre de notre campagne de numérisation, plusieurs autres projets « Industry 4.0 » sont déjà en cours chez Roto. Parmi eux, citons l’enregistrement en ligne des données d’activité des machines et un système de gestion numérique des pièces de rechange. Les technologies testées sur les sites de Roto incluent des robots collaboratifs pour assister la production et l’impression 3D (fabrication additive). Certains collaborateurs testent également des lunettes de réalité mixte (HoloLens).
Évidemment, nous vous en dirons plus dès que ces innovations auront été déployées.
Demandez un entretien
Faites le point avec le représentant Roto de votre région. Laissez-nous vos coordonnées. Il vous contactera pour fixer un rendez-vous.
En remplissant et en soumettant le formulaire ci-dessous vous acceptez notre politique de confidentialité.